食品製造業の改善例「量目(歩留まり)の見える化」の件
お疲れ様です
製造リーマンです。さて今回は製造業の中でも、食品業界における量目管理の見える化改善について記事にしていきます。
#目次#
そもそも見える化(可視化)とは
製造現場における見える化とは、言葉の通り「見えるようにする」ことを手段として、製造ラインの課題を解決する改善の1つとなります。見えるようにするものは様々あり、基本的には現状で不透明で不利益が発生している場所に対して行います。
ここでのポイントは見えるようにすることは「手段」であるという点です。見えるようにすることで得たい先の「目的」を明確にしておくと、見せ方が変わってきます。
見える化の方法
改善したい場所や内容によって見える化の方法は様々ですが、今回は食品業界の製造現場を舞台に一部具体的な例で方法を見ていきましょう。
改善例:数値の見える化
方法:データ送信からのグラフ化
食品製造業の場合、製品形態での重さが必ず設定されています。これを「量目」と呼びます。この量目は製品の出荷基準にもなる為、とても大切な品質基準の1つです。
そして、もう1つ製造企業側としてはこの量目はコスト面としても重要な意味があります。
製造する為には、原材料があり、可能な限り原材料によって製造できる最大製品個数を企業は生産することを目標としています。これを「歩留まり」の管理と呼びます。
歩留まりとは、簡単に言うと製品を100個作るのに必要な原材料に対して、結果何個作れたか、この比率を主にパーセンテージにして表すのが歩留まりになります。
原材料100個分で実際90個の製品が作られれば、歩留まりは90%となります。この時、歩留まりが90%に留まった原因として、不良品の発生や「量目」が関係してきます。
製品1個が100グラム設定だと、マイナスしない為に必ず上乗せ値を設定します。これは企業や職場によって変わりますが、この設定をいかに厳しく管理できるかが、「量目」管理となります。
そして、製造現場で抱えている問題点の1つが作業員ごとの個人差です。個人によって現場の状態を感じる「感度」は異なる為、製造中に歩留まりへの意識をどれだけ高めてオペレーターを行うかは、作業員ごとに異なります。最終的な目的は同じでも作業員は機械ではない為、一定の作業方法や監視体制は取れません。
見える化の実践内容
具体的な問題点としては、大量の連続して流れる製品の「量目」を常に作業員の目で管理するとこが困難であるという点です。人の力だけで、監視、調整を行うには膨大なデータを扱うため、監視している瞬間の状態でしか判断ができず、安定性が著しく欠けてきます。また、安定性だけを取って上乗せ値を多量に設定していては、歩留まりが悪化していき、企業としては高いコストで製品を作り続けることとなります。
ここで、「見える化」です。
量目管理においては、製品の重量を図る機器である「ウェイトチェッカー」を活用します。様々なメーカーがウェイトチェッカーの製品を出していますが、基本的に現代の機器には外部機器にデータを出力する機構が備えられています。詳しい方法は省略させて頂きますが、(メーカーに確認すると方法は教えてもらえます)この出力を利用し、PCにデータを入力することで、1つ1つのデータを点ではなく、「線」で見える化することができます。下記のグラフは見える化の表示例です。1つ1つのデータはあくまでも「点」に過ぎず、この「点」ばかりを見ていると、調整方向を誤り、思わぬ損失を出してしまう可能性もあります。しかしデータの「点」と「点」をリアルタイムで結び付けていき、「線」にすることで、全体の動き(移動平均)が視覚的に判断できます。
また、より見える化として、活用するために、グラフにメモリと上限値、下限値の線を引いておけば、目標値に対する現在の状況が一目で確認できます。
今回の見える化のポイント
グラフ化することで作業員に視覚的に製造ラインの状態を伝達することができ、量目管理、歩留まりに対する「意識向上」には十分に効果的です。実際に安定して製造できていることが見える化されれば、モチベーションの向上にも繋がるでしょう。
そして、今回のポイントですが、見える化することはあくまでも「手段」であり。「目的」の到達ではなく、あくまでもそれに伴う効果の実績が「目的」となります。
データを製造ライン上で見える化することだけがゴールではなく、ここから今まで風景化していた問題点に対して、気づきや解決方法を導き出せると更に、製造ラインの効率化がグっと進みます。
まだ、データ管理できていない部分が自分たちの製造ラインにある場合は、付帯設備の能力を確認して、データ管理だけではなく、見える化にもチャレンジしてみて下さい。
一番簡単な見える化の題材とは
見える化のなかで、一番取り組みやすいのは、目視確認用の見える化になります。これは非常に単純ですが、効果は抜群です。
機器内部の駆動部分で実際に動いている状態を見たい時や、経年的な状態確認を行いたい時に、カバーで蓋をされていると見えません。例えば、こうしたカバーを透明にしていつでも監視できるようにするのです。
カバーを透明化することで、常に目視で確認することができ、定期的なメンテンナンスや注油も可能となり、開けたらびっくりは防止することができます。
カバーの素材はポリカーボネートがオススメです。割れにくく、透明性の高い材質なので、カバーにはとても向いています。
SUS(ステンレス)のアングルと組み合わせても丈夫なカバーが作れるでしょう。
是非、現場で実践してみて下さい。
最後に
製造業は物(製品)を製造するために、様々な部署が存在しますが、もっとも経費がかかるのは製造現場です。要員に伴う人件費や原材料費、設備を維持するためのメンテナンス費、エネルギー費などなど、経費が掛かる分、コストダウン改善による貢献ができるのも製造現場の楽しみです。
様々な視点から今後も製造現場の「改善」について記事にしていきますので、もし参考になれば幸いです。
最後までありがとうございました。
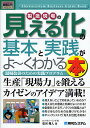
製造現場の見える化の基本と実践がよ〜くわかる本 現場改善のための実践プログラム/石川秀人【1000円以上送料無料】
- ジャンル: 本・雑誌・コミック > ビジネス・経済・就職 > 経営 > 経営戦略・管理
- ショップ: bookfan 2号店 楽天市場店
- 価格: 1,620円